Page 2 of 3
Posted: Mar 06, 2012 11:25 PM
by Shadow
I know but that's what I was getting from Kens explanation.
500hp is ok as long as it's at 15psi.
Posted: Mar 06, 2012 11:37 PM
by turbodan
That would be referring to a different motor. You won't be anywhere near that with an M30 at that boost level. HP correlates to air mass. To move 50lbs/min with a 3.4l M30 you can run more boost or run the engine at higher RPM. Thats all there is to it.
Posted: Mar 07, 2012 12:00 AM
by Ken H.
Shadow wrote:I know but that's what I was getting from Kens explanation.
500hp is ok as long as it's at 15psi.
Depends on everything else in the engine. For example, some monster stationary emergency diesel generators crank well over 500 hp and have a turbo giving 5 or 6 psi. And if needed, they can run for a couple of weeks. Then we see nitro-fueled 750 cc drag bikes running 60 psi and Lawd Knows what kind of rwhp . . . .for about 7.5 seconds.
My engine seems happy as a pig in shit @ 7.25 psi . . . and is doing about 560 and change rwhp.
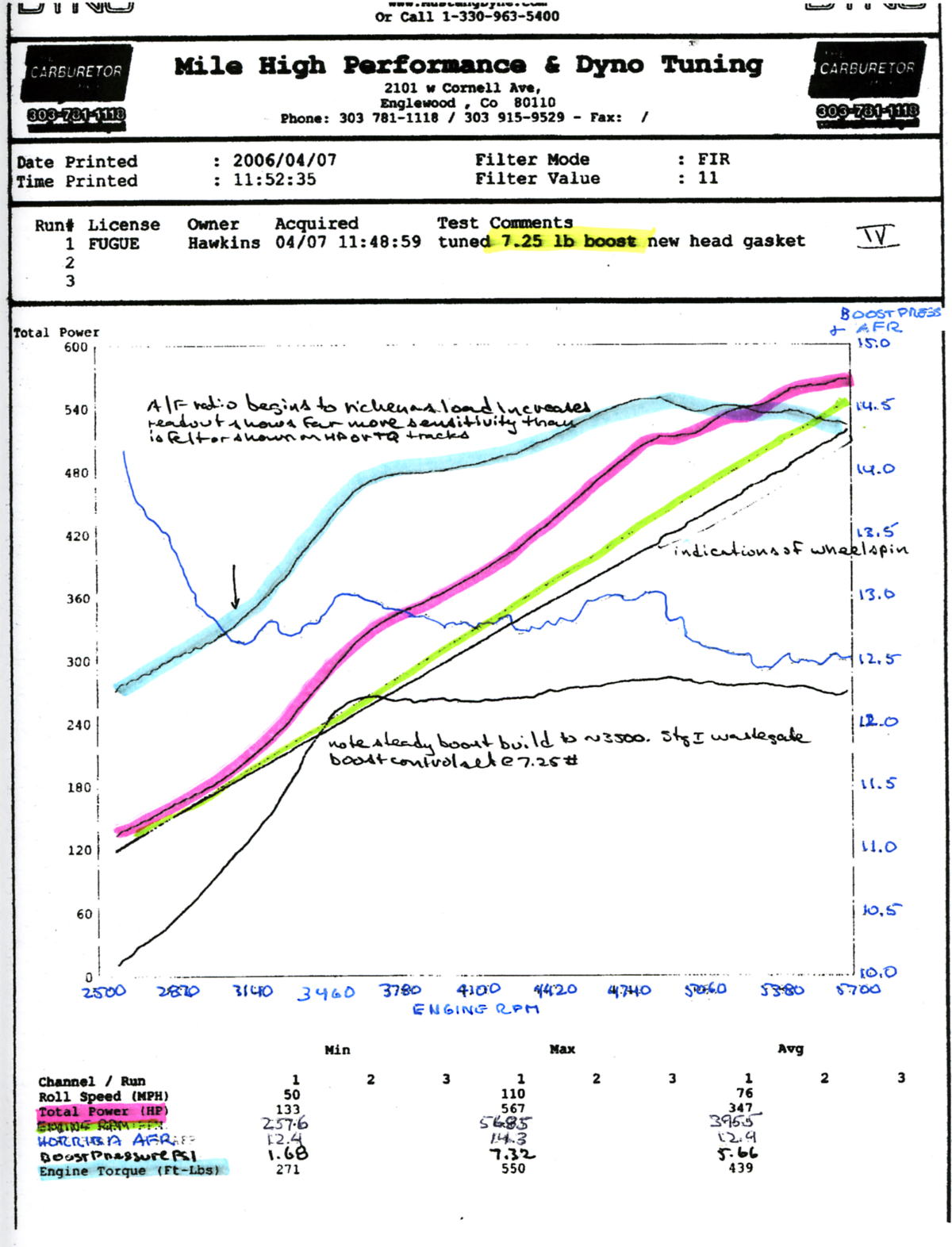
Posted: Mar 07, 2012 12:09 AM
by mooseheadm5
Shadow wrote:I know but that's what I was getting from Kens explanation.
500hp is ok as long as it's at 15psi.
He is speaking about a rule of thumb. If your average M30 is run higher than 15psi, the chances for detonation are much higher, and that is the number one cause of turbo engine damage. If you take steps to reduce detonation through the use of methods like higher octane fuel, updated fuel metering and knock sensing, or methanol injection, that safe boost number can go up. If you ignore good design and run the wrong plugs, no intercooler, and a poorly matched turbo, that safe boost rule of thumb number Ken quoted quickly drops.
The power the bottom end can handle depends on how you make the power. You can't make 500HP on a stock bottom end without boost. Doing so would require stratospheric revs that would break the crank and float the valves. You can do it by moving more air at a lower RPM but that will require forced induction. A motor can be modified to flow as much air at 10psi as an unmodified motor moves at 15psi.If they flow the same amount of air, they will make similar amounts of power (depending on pumping and frictional losses.)
Posted: Mar 07, 2012 1:56 PM
by Ken H.
turbodan wrote:I don't know what it is about high boost that seems to diminish ring life. I've read that its a common issue.
Dan,
This issue, and it is a valid one, goes back to the underlying point that an IC engine is a form of air pump. When you go to FI, you are
de facto putting more air mass into the combustion chamber than you would in a normally-aspirated situation. How much more depends on the increase over atmospheric pressure. Since there are invariably heat and frictional losses in the process, the resulting Density Ratio will be less than the Pressure ratio. As boost (Pr) rises, Dr will increase, but at a decreasing rate.This is why just jacking up boost numbers shows diminishing returns.
But that higher density (pressurized ) incoming charge has had heat added to it via its being compressed. That heat is absorbed in some measure by the surrounding walls of the combustion chamber--head, cylinder walls, piston crown.
That temperature delta causes the metals to expand and to some degree, weaken and distort. In order to prevent those events from affecting the piston rings, especially the top one, four steps can be considered.
1.
Change the piston material. This is one reason why forged pistons are used. The forging is a usually somewhat denser than cast aluminum and has different alloying elements in it, the better to reduce coefficient of expansion and maintain strength at a stipulated temperature.
2.
Use a coating with high resistance to heat transfer. Ceramic coating of areas exposed to burning exhaust gases--valves, combustion chamber roof, exhaust track, piston crown. Cutting the heat transfer allows the energy in the form of heat to be kept in the exhaust gas and sent onward to rotate the turbine.
3.
Thicker piston crown. This reduces distortion and weakening at combustion temperatures. This is most apparent where the piston has immediate exposure to the combustion flame front--crown, squish area and the ring at the top of the piston sidewall between the crown and the top of the first ring groove.
4.
Move the location of the top ring groove further down on the side of the piston. If the piston's geometry permits, lowering the ring groove means the top ring's upper land is thicker and less prone to heat distortion. Given that we are trying to find space for two compression rings, an oil scraper ring and access for the wrist pin, things tend to get a tad crowded.
So to oversimplify things a bit, going to 1 bar of boost is trying to get 7 liters of air movement out of a 3.5 liter displacement motor. Looking at Charles's Law for gases, V1*T2 =V2*T1, Cramming twice as much fresh charge into the combustion chamber space is going to increase temperatures. A lot. As that temperature rises, we have both a weakening of the metals and a greater propensity for potential premature burning of the charge--detonation.
Somewhere in my files I have some photos of an F1 piston. The top ring is nearly 12 mm below the piston crown vs. around 8 mm in a normal street engine. This was done specifically to address the heat problem.
All this being said, the rings, especially #1 take a beating. Not dissing anyone's schooling at Hardnox U., but working through this stuff on paper before spending one's coinage saves a great deal of aggravation. So with all due respect to Todd D., paying attention to the "5 P's Rule" seems to be a good idea.
Posted: Mar 07, 2012 4:58 PM
by FirstFives Dictator
What I take away from this is start off with great flow first. Otherwise the square root relationship between boost and HP will starting diminishing returns.
At 1.68 psi Ken's motor is putting out 271 ft lbs of tq
Posted: Mar 07, 2012 5:07 PM
by turbodan
Intercooling plays a large part in the discussion. Insufficient charge cooling capacity would definitely cause problems with elevated boost levels. I would expect detonation to present a more immediate problem with high manifold air temps and high boost.
I like this online calculator for visualizing pressure and density ratios:
http://www.stealth316.com/2-turbotemp.htm
I'm simply not capable of making these calculations on my own. Good thing this gentleman was kind enough to set it up.
In my case, with what I would consider to be ample intercooling capacity, I manage an overall density ratio of about 2.5x at 1.4 bar with manifold air temps within ten or twenty degrees of ambient. The key is holding down intake air temps. Any air density lost due to heating can be recovered by cooling. I consider some pressure drop through the intercooler to be a fine trade off for near ambient charge temps.
I do wonder about the effect of exhaust manifold pressure on the equation. High boost necessarily increases exhaust manifold pressure. I suppose depending on how well balanced the intake and exhaust manifold pressures are that could result in poor scavenging, dimished VE and additional heat in the combustion chamber. It seems likely that exhaust manifold pressure would exceed intake manifold pressure on most turbo systems, which would be more and more of a problem as boost increases. In applications with an oversized turbine and efficient manifold I would imagine that boost could blow through during overlap and scavenge the combustion chamber very efficiently.
Posted: Mar 07, 2012 5:07 PM
by T_C_D
Ken,
Is that graph corrected for the altitude? If so, what is the actual rwhp?
Posted: Mar 07, 2012 5:12 PM
by Ken H.
FirstFives Dictator wrote:What I take away from this is start off with great flow first. Otherwise the square root relationship between boost and HP will starting diminishing returns.
At 1.68 psi Ken's motor is putting out 271 ft lbs of tq
MmmmmmYeh. Power delivery as one moves from vacuum into boost is pretty understated until it hits a bit under 4 psi. Keep yer leg in it and it has this tendency to get one's undivided attention.

=>

=>

=>

Open the boost controller to allow boost to go from 7.25 to 15 and it has been favorably compared to a shot off the #2 cat on the USS Enterprise.
Posted: Mar 07, 2012 5:13 PM
by turbodan
FirstFives Dictator wrote:What I take away from this is start off with great flow first. Otherwise the square root relationship between boost and HP will starting diminishing returns.
At 1.68 psi Ken's motor is putting out 271 ft lbs of tq
Thats one thing I enjoy about forced induction. You can take a stock, reliable engine and just add boost to make power. The expense of taking the steps required to open up the motor to breate more efficiently aren't required to reach very high power levels. You also avoid sacrificing reliability by leaving the valvatrain and block stock.
Posted: Mar 07, 2012 5:32 PM
by Ken H.
turbodan wrote:Thats one thing I enjoy about forced induction. You can take a stock, reliable engine and just add boost to make power. The expense of taking the steps required to open up the motor to breathe more efficiently aren't required to reach very high power levels. You also avoid sacrificing reliability by leaving the valvatrain and block stock.
vulvatrain??

More or less true, but the heat and mechanical stresses can't be avoided. I don't know where the "crossover" point is, but I would think that good engineering on the NA motor would supply a fair margin of safety on engine reliability. Maybe 5-6 psi, and that for only short periods.
Posted: Mar 07, 2012 5:58 PM
by Kenny
Ken H. wrote:
1. Change the piston material. This is one reason why forged pistons are used. The forging is a usually somewhat denser than cast aluminum and has different alloying elements in it, the better to reduce coefficient of expansion and maintain strength at a stipulated temperature.
Afraid you back that backwards. Coefficient of expansion is HIGHER for a forged piston, and they require substantially MORE piston to wall clearance. They are stronger at higher temps, but the melting point is not really much different.
On other words, in the case of lean mixtures toasting a pistons, forged won't save you.
The rest of your post neglects a few important concepts - the most important being that pistons are actually pretty well insulated from "normal" combustion temperatures by way of what is known as a gas boundary layer.
One thing that detonation does is it disturbs this boundary layer and allows the piston to be "exposed" the the full heat of combustion.
Changes in piston design, material, and coating, can in some cases buy a small amount of forgiveness in these circumstances, but it is small.
A bad tune will break even the fanciest components. A good tune will allow even pedestrian parts to live under very high outputs.
Not saying the design considerations you listed aren't valid, but the tendency is to overstate these and understate the need for good engine control.
Per my sig, my 2.8L volvo inline 6 made 540whp on pump gas with stock cast pistons, no probs. I also had a mishap in my early days of the tuning learning curve and broke a piston at 12psi and probably 350whp. Lots of people would say "oh you need forged pistons". What I needed was to calibrate the engine controls correctly.
Posted: Mar 07, 2012 6:11 PM
by Ken H.
turbodan wrote:Intercooling plays a large part in the discussion. Insufficient charge cooling capacity would definitely cause problems with elevated boost levels. I would expect detonation to present a more immediate problem with high manifold air temps and high boost.
I like this online calculator for visualizing pressure and density ratios:
http://www.stealth316.com/2-turbotemp.htm
I'm familiar with this. Nice item. I'm simply not capable of making these calculations on my own. Good thing this gentleman was kind enough to set it up.
In my case, with what I would consider to be ample intercooling capacity, I manage an overall density ratio of about 2.5x at 1.4 bar with manifold air temps within ten or twenty degrees of ambient. The key is holding down intake air temps. Any air density lost due to heating can be recovered by cooling. I consider some pressure drop through the intercooler to be a fine trade off for near ambient charge temps.
IC pressure drops come with the territory. Some of it can be avoided by proper ingress and egress tubing sizing and minimizing piping bends.
In a lot of cases, the sizing of the IC core is dictated by location, with the result of the core being undersized for the known airmass being put through it. This means the air mass may not be cooled as much as is desirable, equaling higher-than-optimal IATs.
Designing the IC system is a somewhat involved topic and needs to be prattled on about in another thread.
turbodan wrote:I do wonder about the effect of exhaust manifold pressure on the equation. High boost necessarily increases exhaust manifold pressure. I suppose depending on how well balanced the intake and exhaust manifold pressures are that could result in poor scavenging, diminished VE and additional heat in the combustion chamber. It seems likely that exhaust manifold pressure would exceed intake manifold pressure on most turbo systems, which would be more and more of a problem as boost increases. In applications with an oversized turbine and efficient manifold I would imagine that boost could blow through during overlap and scavenge the combustion chamber very efficiently.
Good observations. The residual exhaust manifold pressure issue gets some coverage if you look at Garrett's graphs for their larger GT units. These show what kind of exhaust manifold pressures need to be considered. For example, looking at a GT-3582R (which is Not Bad for an M30), using a Pressure Ratio of 2.25, it shows a turbine flow of around 26#/min. In turn, this implies robust exhaust gas scavenge. To get there, it is almost mandatory to have a tuned tubular exhaust system. Valve overlap may help somewhat, but probably not enough to do the job.
I ought to add that changes in Ve have very substantial effects on overall power generation. The other major elements are A/R and Brake Specific Fuel Consumption. To see what effects these have, try running your motor's numbers through the
http://www.not2fast.com turbo calculator.
This little exercise is both sobering and worthwhile.
In messing with this stuff, I came away thinking that people put a lot of time and money into the intake side--turbos, manifolding, etc. MAJOR bling factor. Not so much on the exhaust, absent stepping up for a tubular arrangement. But getting the spent charge outta there may be as important or more so than cramming any amount more charge into the hole.
Ve is heavily influenced by air mass movement, but if the incoming charge is degraded by mixing with unremoved burnt gases, what have we accomplished?
So I look awfully hard at what kind of scavenge the head and the exhaust system can offer. We may have a more efficient motor with a smaller turbo compressor, an IC the size of a Manhattan apartment, and an exhaust system that will pull the paint off the firewall.
my $.02.
Posted: Mar 07, 2012 6:22 PM
by Coldswede
Here we have it folks, one of those epically fine discussions MyE28 is famous for! I've learned a lot already.
I have a question about "Choke". Is Choke solely determined by the design and limitations of the Turbo or is it a complicated problem based on the turbo, intake system and flow characteristics of whatever engine is used?
Posted: Mar 07, 2012 6:24 PM
by Ken H.
Kenny wrote:Ken H. wrote:
1. Change the piston material. This is one reason why forged pistons are used. The forging is a usually somewhat denser than cast aluminum and has different alloying elements in it, the better to reduce coefficient of expansion and maintain strength at a stipulated temperature.
Afraid you back that backwards. Coefficient of expansion is HIGHER for a forged piston, and they require substantially MORE piston to wall clearance. They are stronger at higher temps, but the melting point is not really much different.
On other words, in the case of lean mixtures toasting a pistons, forged won't save you.
This is all true. My Bad. I'm aware of the clearance requirement point, Ken. Just didn't think it through. Pobody's Nerfect.
The rest of your post neglects a few important concepts - the most important being that pistons are actually pretty well insulated from "normal" combustion temperatures by way of what is known as a gas boundary layer.
One thing that detonation does is it disturbs this boundary layer and allows the piston to be "exposed" the the full heat of combustion.
Changes in piston design, material, and coating, can in some cases buy a small amount of forgiveness in these circumstances, but it is small.
True, dat.
A bad tune will break even the fanciest components. A good tune will allow even pedestrian parts to live under very high outputs.
Not saying the design considerations you listed aren't valid, but the tendency is to overstate these and understate the need for good engine control.
Not to belabor the point, but in doing the dyno tuning, one can manage both A/R and ignition timing quite closely. Keep the A/R on the rich side as kPa goes up and you avoid lean burn and detonation. Back of the ignition advance as the knock sensor lights up==> avoid detonation. Happy engine.
Kenny wrote:[Per my sig, my 2.8L volvo inline 6 made 540whp on pump gas with stock cast pistons, no probs. I also had a mishap in my early days of the tuning learning curve and broke a piston at 12psi and probably 350whp. Lots of people would say "oh you need forged pistons". What I needed was to calibrate the engine controls correctly.
Posted: Mar 07, 2012 6:35 PM
by Ken H.
Coldswede wrote:I have a question about "Choke". Is Choke solely determined by the design and limitations of the Turbo or is it a complicated problem based on the turbo, intake system and flow characteristics of whatever engine is used?
"Choke," as it is used here, is defined by the design of the compressor and it's impeller wheel.
Pull up a compressor map--go to
http://www.turbobygarrett.com and do a bit of wandering around.
Choke happens when the air mass in the compressor snail essentially goes into a "stall" condition, and isn't moving properly towards the IC and intake plenum. This is indicated by the rapidly decreasing efficiency percentages on the "topographic map" that constitutes the compressor's outputs.
OTOH, on the far left-hand side of the compressor map, we see the "Surge" region, where the pressures and the air mass are below what the impeller can "sink it's teeth into." In that case, air can be pushed back into the compressor from higher pressure regions such as the intake plenum or IC, and the unit "hiccups."
Posted: Mar 07, 2012 6:36 PM
by cvillebimmer
This thread is full of win. Thank you to all who know more than I do and your willingness to share.
Posted: Mar 07, 2012 6:50 PM
by Ken H.
T_C_D wrote:Ken,
Is that graph corrected for the altitude? If so, what is the actual rwhp?
Yes. The graph shows an SAE corrected value, taking into account altitude, relative humidity and ambient air temperature. These corrections amount to about 17%. Someplace in my files I have all the hard numbers. So the shown 567 rwhp is actually around 470-471. Before one goes off on this,
any motor, brought up to Denver from sea level will show comparable decreases. The purpose of the SAE corrections is to allow 1-to-1 comparisons regardless of a dyno's location.
Note also that the 567 is rwhp. Apply the commonly-accepted manual tranny drivetrain losses factor of 16% and fwhp is ~675 in a sea level environment.
Posted: Mar 07, 2012 7:56 PM
by turbodan
Its just too easy to apply corrections. Uncorrected is the best way to evaluate performance. My 2.7 M20 made 384rwhp uncorrected here in Abq. It wouldn't feel right quoting the corrected figure, 468 IIRC, or the corrected flywheel number, 548 HP. That makes for a pretty big spread, and I like the real, measured number best. The motor might genuinely make more power at sea level, or I might have to turn the boost down because it wouldn't support the additional combustion chamber pressures from the denser atmosphere.
Perhaps I'm just sick of the bullshit when it comes to bench racing. Nothing is ever quoted conservatively. I'm happy to say I made "only" 384 rear wheel. My horses are just bigger than everybody elses.
Posted: Mar 07, 2012 7:57 PM
by Mark 88/M5 Houston
Thank you gentlemen, a very interesting and educational thread.
Posted: Mar 07, 2012 10:18 PM
by Ken H.
turbodan wrote:Its just too easy to apply corrections. Uncorrected is the best way to evaluate performance. My 2.7 M20 made 384rwhp uncorrected here in Abq. It wouldn't feel right quoting the corrected figure, 468 IIRC, or the corrected flywheel number, 548 HP. That makes for a pretty big spread, and I like the real, measured number best. The motor might genuinely make more power at sea level, or I might have to turn the boost down because it wouldn't support the additional combustion chamber pressures from the denser atmosphere.
Perhaps I'm just sick of the bullshit when it comes to bench racing. Nothing is ever quoted conservatively. I'm happy to say I made "only" 384 rear wheel. My horses are just bigger than everybody elses.
Dan'l, would you feel any better if you dyno'ed your engine at Leadville (10,152')? The number would be smaller, but no more or less accurate. Similarly, how do you feel about the speeds that come off of Bonneville (4,219 ft)? Are these incorrect because they were obtained at something other than sea level?
The entire purpose of the SAE algorithm is to account for tests taken in different locations and under different conditions.
The key variables--altitude, relative humidity and ambient temperature are subject to highly accurate measurement.
I will cheerfully grant that dynos can be and often are run in a manner that gives specious results. But if two machines at different locations are both properly set up and calibrated, you are going to get highly comparable results.
I'll agree about the horseshit that gets handed out in bench racing sessions. But when the pulls are done with the objective of getting the engine properly dialed in, the Hp/Tq values are a metric which summarizes all of the work that's been put into the project. And yeah, 468 sounds better than 384.

I might add that I am highly skeptical of calculated fwhp numbers....there is just too much room for fudge factor in the process.
That help?
Posted: Mar 07, 2012 10:37 PM
by mooseheadm5
The point I think Dan is making is that just because an engine is tuned to make 500 corrected rwhp at a certain air density/temp/etc. doesn't mean that it will necessarily be able to make 500 rwhp when brought down to sea level. Fuel requirements change, intercooler temps change, etc. so a person may find that their fuel pumps and injectors are undersized or that their compressor doesn't operate at sea level at the same level of efficiency as it does at higher altitudes. Using the corrections when they are comparing the same motor to itself at the same dyno is a perfectly reasonable thing to do. Using the corrections when they amount to double digit percents (and nearly triple digit whp figures) seems to be what makes Dan uncomfortable.
Posted: Mar 07, 2012 10:46 PM
by Kenny
mooseheadm5 wrote:The point I think Dan is making is that just because an engine is tuned to make 500 corrected rwhp at a certain air density/temp/etc. doesn't mean that it will necessarily be able to make 500 rwhp when brought down to sea level. Fuel requirements change, intercooler temps change, etc. so a person may find that their fuel pumps and injectors are undersized or that their compressor doesn't operate at sea level at the same level of efficiency as it does at higher altitudes. Using the corrections when they are comparing the same motor to itself at the same dyno is a perfectly reasonable thing to do. Using the corrections when they amount to double digit percents (and nearly triple digit whp figures) seems to be what makes Dan uncomfortable.
Very well said. I am with Dan, in the context of forced induction engines Anyway. With normally aspirated vehicles SAE is 100% legit, but with forced induction it needs a grain of salt.
Posted: Mar 07, 2012 11:14 PM
by Ken H.
mooseheadm5 wrote:The point I think Dan is making is that just because an engine is tuned to make 500 corrected rwhp at a certain air density/temp/etc. doesn't mean that it will necessarily be able to make 500 rwhp when brought down to sea level. Fuel requirements change, intercooler temps change, etc. so a person may find that their fuel pumps and injectors are undersized or that their compressor doesn't operate at sea level at the same level of efficiency as it does at higher altitudes. Using the corrections when they are comparing the same motor to itself at the same dyno is a perfectly reasonable thing to do. Using the corrections when they amount to double digit percents (and nearly triple digit whp figures) seems to be what makes Dan uncomfortable.
Paul, I'll agree with your statements, except for the last one. The purpose of the SAE algorithm is to do precisely that...to permit comparable results to be tabulated under highly disparate conditions.
Break the key elements out and each of them can be and is precisely measured. Where the resulting corrections become sizable, it is easy to understand why one becomes uncomfortable.
What happens w/r/t how various components act/interact/fail to act doesn't change the underlying physics. Which is why when the guys running Funny Cars set up for Pomona arrive at Bandimere, there is wholesale retuning required.
An example on corrections:
1. Sea level air pressure =14.7 psi. Air pressure at the Mile High shop, 5328'. = 12.08 psi. difference =17.82%. This number 12.08 psi may change if a cold front comes through or we have a summer high pressure cell, but the delta will be small.
2. Relative Humidity. Assumed to be 77 deg F and 20% r.h. for the moment. This creates about 6 millibars of additional air pressure due to drier air being more dense. Air pressure @ 5328" = ~812 millibars. 6/812 = .0074, or about 3/4 of 1% density difference.
3. Air temperature. Assume 72 deg F. The SAE "algorithm number" is 59 deg. F. so we are 13 degrees warmer. 13 deg F = ~7.22 deg Celsius. A commonly used rule of thumb is 1% power loss for every 7 deg C. temperature rise. 7.22/7.00 = 1.0314. So a loss of about 1.0314%.
These factors are
multiplicative in nature.
Using the "residual" from the losses (or gain in the relative humidity), we have .8218 x 1.0074 x .9686 = .80189. Or a correction factor of ~19.81%.
The SAE algorithm is a bit more involved, but what this says is an engine which will turn out 500 hp at sea level, under SAE's stipulated conditions, will deliver about 409 hp on a dry spring day in Denver. Or Albuquerque. Probably a bit more in ABQ. The horses are bigger there. <<TIC icon here>>
Posted: Mar 07, 2012 11:33 PM
by mooseheadm5
Ken H. wrote:
The SAE algorithm is a bit more involved, but what this says is an engine which will turn out 500 hp at sea level, under SAE's stipulated conditions, will deliver about 409 hp on a dry spring day in Denver. Or Albuquerque. Probably a bit more in ABQ. The horses are bigger there. <<TIC icon here>>
I disagree. Section 5.5 of SAE1349 (the standard corrections used nowadays.) Pretty much says not to use these correction factors on turbo compensated engines.
What correction methods were being used?
The SAE also disallows corrections greater than ±7%.
Posted: Mar 07, 2012 11:48 PM
by turbodan
SAE comes up at 20% at ~5500 feet. Too much IMO.
I was definitely referring to turbo dynos. NA cars are affected in a much more predictable manner.
Posted: Mar 08, 2012 12:04 AM
by Ken H.
turbodan wrote:SAE comes up at 20% at ~5500 feet. Too much IMO.
Altitude alone will do it. you lose ~3.3% air pressure per 1000 ft elev. gain. 5500 ft ASL = 12.00 inches pressure. 12.00/14.7 = 18.4% pressure loss. This leaves you 1.6% for rel humidity and temperature. Entirely reasonable.
turbodan wrote: I was definitely referring to turbo dynos. NA cars are affected in a much more predictable manner.
Posted: Mar 08, 2012 12:07 AM
by mooseheadm5
So you are saying that the pressure at the inlet valves is 18% less because you are at a higher elevation? That may be true of an NA car, but your car is boosted so the pressure at the intake valves (when in boost) is whatever you set your boost control to.
I say stand on your measured rwhp numbers. They are impressive and do not rely on potentially flawed correction factors.
Posted: Mar 08, 2012 12:23 AM
by Ken H.
mooseheadm5 wrote:
What correction methods were being used?
The SAE also disallows corrections greater than ±7%.
Using the SAE J1399Aug04 formula, the correction is:
Cf = 1.176{(990/Pb) * [Tc+273/298)]^.5] - .176
where
Cf = correction factor
Pb = ambient dry air pressure, in millibars
Tc = ambient temperature in degrees Celsius
12.08 psi = 832.9 millibars (
http://www.digitaldutch.com)
Using the above,
Cf = 1.176 {[990/883+4)] * [(19+273)/298]^.5} -.176
(990/837) = 1.1828. (292/298) = .9799. .9799)^.5 = .9899.
1.1828 * .9899 = 1.1708
1.176 * 1.1708 = 1.3769 1.3769 - .176 = 1.2009
So all things being equal, a NA motor running at MHP under the 4/7/06 test conditions should generate 79.91% of its sea level (actually SAE standard conditions) Multiply the observed values at altitude (i.e., @ MHP) by 1.2009 to correct for altitude, relative humidity and temperature.
Mile High elevation = 5328’. Ambient pressure = 12.08 psi. Sea level pressure = 14.7 psi.
12.08 / 14.7 = .8218, or a 17.72% correction for air density. This is a bit off from the 20.09% value, leaving 2.37% for temperature and relative humidity corrections.
However, all of these calculations apply to NA engines; FI is a different case.
A turbo applies its compression on the air in the compressor, having been taken in at ambient pressure. So pressure correction for FI is taken as
(ambient psi + boost psig) / (sea level psi + boost psig)
Ambient pressure = 12.08. Boost = 14.95 psig. Sea level ambient air pressure = 14.7 psig.
I Googled horsepower corrections altitude and found this website:
http://www.mazda3forums.com One of the posters had a really good succinct description of the formulas we’ve been hacking at. “Ah, gestalt!”
(12.08+14.95) /(14.7+14.95). 27.03 / 29.65 = .9116. So the air density correction values should be ~8.84% lower than what an equivalent sea level pull would show (ignoring any temp and RH effects). Add back the 2.37% in the above and we have 8.84 +2.37 = 11.21% correction.
What this all says is dyno readings done on turbo motors at altitude will show less of a correction to a stipulated sea level power level.
But SAE is silent on the topic.
Posted: Mar 08, 2012 8:06 AM
by T_C_D
Ken,
The fact is that your car doesn't drive around with SAE corrected HP and therefore all your mention of it in a comparison manner for reliability, clutch capacity, etc isn't relevant. What was the uncorrected rwtq? 440/450ish?
Todd